Case Studies
This little tag tells an incredibly
valuable story.
2012.
That’s the last time we repaired this pump.
Our repairs normally last years, even with the abuse some of these pumps have to take day in and day out. And the 5 year example in this case is pretty typical.
Case in point
In February of 2012, a customer needed their Dean ANSI pump repaired. Our repaired pump made it 5 years before needing work!
“These guys go above and beyond!”
Gary Morrison
Maintenance Planner
Catalyst Division
Clariant Corporation
What do we do differently?
Look at the check list (below). Upon receipt, the problem pump is checked and each dimension and value is documented. This gives us a baseline as to the extent of repairs needed. Any component that is not within specification is recommended to be replaced or repaired. Then after authorization to repair, the replaced or repaired components (and finished complete assembly) is rechecked to verify all meet factory recommended specifications.
If a customer desires or something non-typical occurs, pictures of the subject part or parts are taken and furnished to the customer.
Not everyone or every repair needs this level of detail, but we can provide it if you desire.
We not only can bring pumps and parts up to OEM specs, we often surpass those specs, including dealing with tolerances within 1/10,000 of an inch.
We’ve even gone so far as to make duplicates of hard to find parts.
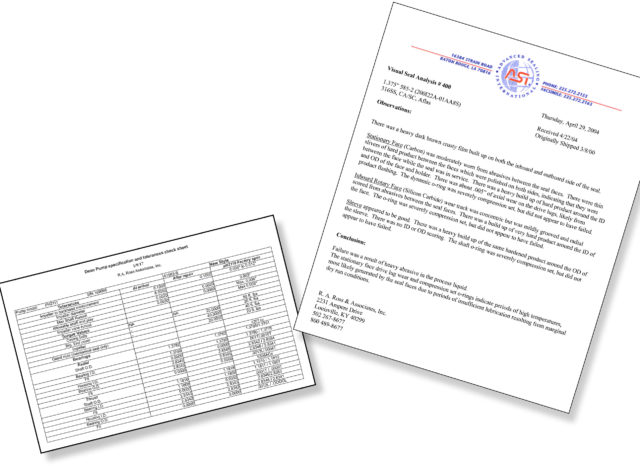
Attention to detail
No repair leaves our shop without passing a rigorous checklist. This attention to detail will save you valuable downtime and money.
If you want it repaired right,call us. We’ll arrange shipping, work up estimates and turnaround time, and call you with any concerns about future issues or why your pump or pump parts failed (see evaluation at upper right).
Download the case study
SN169066 ASI analysis
Tolerance Sheet Table 1
Case Studies
Saving money with what is really needed
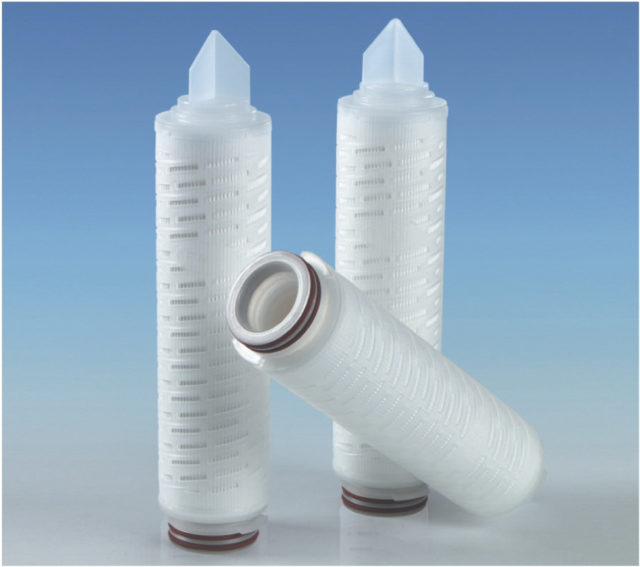
The Pali Emflon filter shown above is perfect for certain situations, but was an expensive overkill for our customers needs.
Another example of how our
knowledge of your industry and
needs saves time and money.
Our solution saved our customer almost $3600 plus quicker delivery
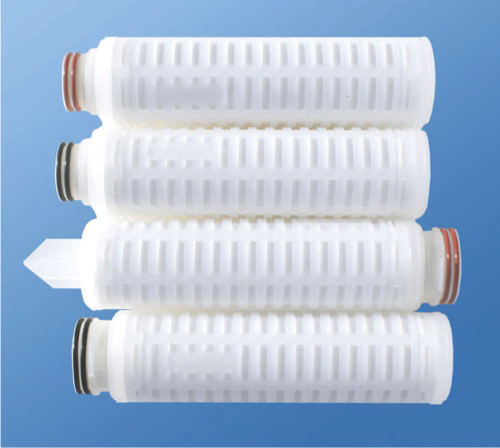
The Graver filter shown is a perfect solution for our customer at a savings of $300 per filter and
saved three weeks of delivery time.
Customer was using a Pall Emflon series Teflon membrane filter that is marketed for the pharmaceutical and biotechnology industries as a tank vent filter in a fermentation process. While the Emflon filter is “technically” suited for this application, it was massive overkill for the service. We were able to provide a Graver TefTEC series Teflon membrane filter that was a third the price, had the same 0.2 micron absolute rating, same materials of construction, and only negligible difference in surface area (8.5 sqft vs. 8.6 sqft) as the Pall filter. The main difference between the filters is the Pall uses a double layer Teflon membrane where the Graver uses a single layer Teflon membrane. The double layer membrane of the Pall filter is what makes it overkill for the application and is how and why the Pall filter is marketed as a pharmaceutical and biotechnology filter. The elimination of the double layer membrane (and a filter that does not have the Pall name on it) allowed us to save the customer nearly $300 per 10” filter and still give them the filtration level and quality they need and deserve. Plus we were able to provide these filters in 5-7 business days vs. 30 business days for the Pall filter! For this single order of 12 filters we saved the customer almost $3600 and weeks of waiting for their filters.
Download the case study
Case Studies
Major natural gas company now has less filter clogging and increased production
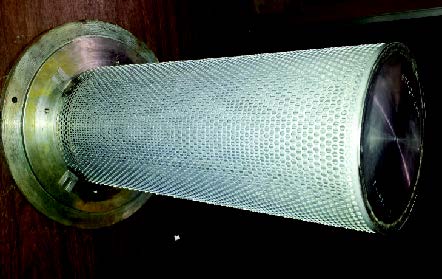
Our pleated filter solution doubles the filter surface
area, while our perforated mesh cover increases
flow and prevents the filter element from clogging.
Problem: Our customer, a major natural gas company refinery, had problems with filter elements clogging
and elements not working efficiently. This increased their downtime and decreased the production.
We were able to replicate the customer’s design. However, we created a pleated mesh filter with a higher micron rating with a perforated shell to increase flow and prevent elements from clogging up quickly.
Not only did we provide a custom filter that would work more efficiently, we were also able to fabricate this filter locally and saved the customer downtime and costs.
Download the case study
Case Studies
R. A. Ross solves magnetic drive pump shell rupture issues for paint manufacturer pumping butyl acrylate
Major paint manufacturer now has significantly
less downtime and has saved valuable product
Problem: A well known aftermarket automotive paint manufacturer was having mag-drive pump failures due to containment shell rupture. The failure prone pump was a Gould’s PTFE lined ductile iron magnetic drive pump with non metallic internal components pumping Butyl Acrylate. The issue was that the Butyl Acrylate would “wick” into the resin that held the containment shell together causing it to weaken enough to rupture. The solution was simply a metallic containment shell, however Gould’s does not offer this. We turned to Dickow for an all metallic 316ss pump with Hastelloy containment shell from their KM close-coupled magnetic-drive series. The all wetted 316ss construction of the Dickow pump also gave the customer the advantage of the external portion of the pump being compatible with their product. On separate occasions the customer had issues with product leaking on the external components via a containment shell rupture or leaking flange gasket causing external pump damage where the pump was not compatible.
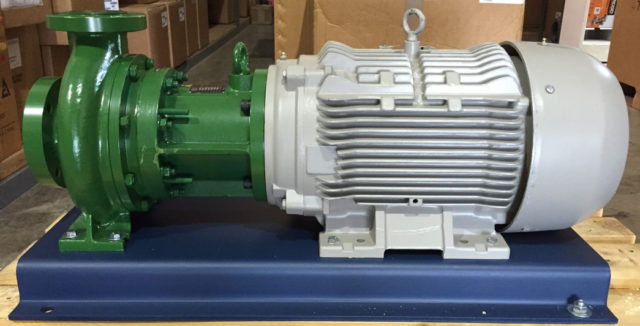
The Dickow close-coupled seal-less all metallic 316ss pump with Hastelloy containment shell. For details, see page 2.
Dickow offers containment shells in a variety of materials including 316ss, Hastelloy, cast titanium, ceramic (Zirconia), and PEEK. While this selection provides near limitlessness for chemical compatibility, the shells are also designed to provide minimum eddy current loss between the drive and driven magnet, resulting in improved efficiency and reduced HP consumption.
Customer Application:
Butyl Acrylate
Ambient to 85 deg. F
200gpm @ 152’ tdh
Pump Selection:
Dickow KMBh
3x2x8.5
316ss – casing and impeller
316Ti ss – pump shaft, driven rotor, and containment shell flange
Hastelloy C – containment shell
Silicon Carbide – Shaft sleeve and thrust bearing
PTFE o-rings throughout pump
Download the case study
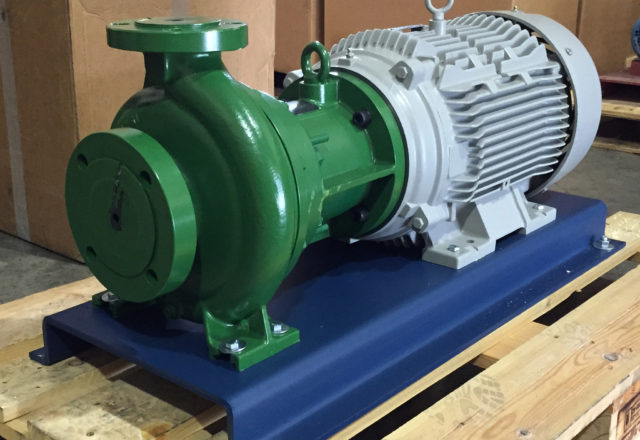
Case Studies
The R. A. Ross team knowledge of pumps and chemical issues solves crystallization problem.
Situation: A well known drywall manufacturer in southern Indiana was having an issue with an air operated diaphragm pump which was being used to inject a dispersant chemical into the wallboard fabrication process. The issue with the diaphragm pump was that the dispersant had a tendency to set up and “crystallize” in the pump and cause the diaphragms to rupture.
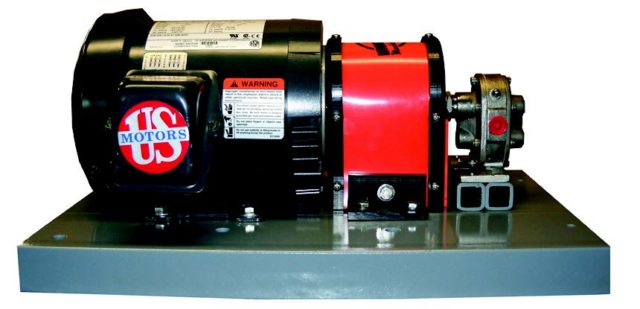
Lobee stainless steel gear pump model 2LOE w/ ¼-HP, 1150 RPM motor: Operating a 3 GPM @ 45’ TDH, ambient temp.
Solution: We recommended a small stainless steel Lobee gear pump that would hold less product in the pump and had the capability to shear any crystals that may have been formed in the liquid while the pump was not running.
The customer has been very pleased with the result and the pump has been in operation for approximately 3 years.
Download the case study