Case Studies
Custom Part Duplication
The R. A. Ross team goes above and beyond to keep you up and running
PROBLEM/SOLUTION:
Our customer was in need of a part for an older pump and faced with long leadtimes and high costs. The part needed was a custom machined eyebolt, not an off the shelf hardware store type item, and had a 10-12 week leadtime at a cost of over $400.
With one of the customer’s parts as a template R.A. Ross was able to work with one of our vendors to have the part duplicated at less than half the cost and reduce the leadtime to approx. a third of the OEM. While this was a significant savings to the customer for one it was a tremendous savings as they purchased 5 of them. The custom duplication process also gave them the option to select whatever material they wanted; carbon steel, 316ss or 304ss.
Download the case study
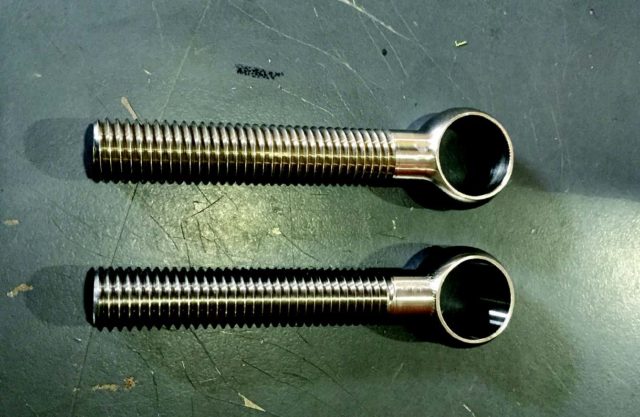
Original part – Top bolt Duplicate part – Bottom bolt
Case Studies
The R. A. Ross team solves repair turnaround time by at least half or better
Problem: Long lead times on repair parts making turnaround times for repairs extremely long.
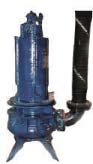
Wemco model 4×11 CES, 30 HP, 120 GPM @100’ TDH, pumping coal slurry.
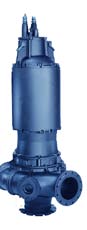
Wemco immersible model
E4K Hidrostal, 30 HP, 120 GPM @100 TDH,
pumping coal slurry.
Solution: A major energy company in southwest Indiana was having issues getting their Wemco submersible pumps that they use in their coal yard serviced in a timely manner. The repair company they were using was having trouble with long lead times on repair parts making the turnaround times for the repairs extremely long. After securing an appointment with the appropriate personnel, we were able to get an opportunity to repair one of the pumps as a trial to see how we could do. We also agreed to stock the appropriate repair parts in our facility to eliminate the long lead time for factory parts. We were able to cut the pump repair turnaround times by at least half or better and have repaired several pumps to date. In addition to the repairs, our quality work and customer service have earned us new replacement pump business as well.
Customer also purchased the E4K Hidrostal with the immersible motor for the “run in air” capability on the occasion when the water level drops below the level of the motor.
WEMCO®-Hidrostal®
The screw/centrifugal impeller with open channel design combines the clog-resistant features of a vortex pump and the high efficiency of a centrifugal pump. The screw section of the WEMCO®- Hidrostal® pump performs like an Archimedes spiral. In thick sludges, slurries, and suspended solids, it burrows like a corkscrew to start the material pumping and keep it pumping. The centrifugal section produces steep head-capacity curve for non-overlaping performance. Combined, the screw/centrifugal action provides high, hydraulic efficiences and clog-resistant pumping. The pump is able to handle large soft solids with efficiencies of more than 80 percent.
Download the case study
www.weirpowerindustrial.com/Wemco
wsprfq@weirgroup.com
Case Studies
Chicken processing plant upgrades and saves money through R. A. Ross & Weir
When R.A. Ross & Associates introduced a local chicken plant to the WEIR WEMCO® Self-Primer pump they were very excited by what they saw. The tool-less, shimless impeller adjustment, the Buzz Saw wear plate, and superior materials of construction were among the main features they liked… and wanted! However, with relatively new self-primer pumps from a different manufacturer in use, the chicken plant could not justify the cost of replacing each unit. With its “one step ahead” style of thinking WEIR had that problem solved. When designing the WEMCO® Self-Primer, other industry standard pumps were taken into consideration. The rotating assembly in the WEMCO® Self-Primer pump was a direct replacement for the pump casing currently in use, making it possible to upgrade each unit to have the benefits of the WEMCO® Self-Primer at a lower cost than replacing the entire pump.
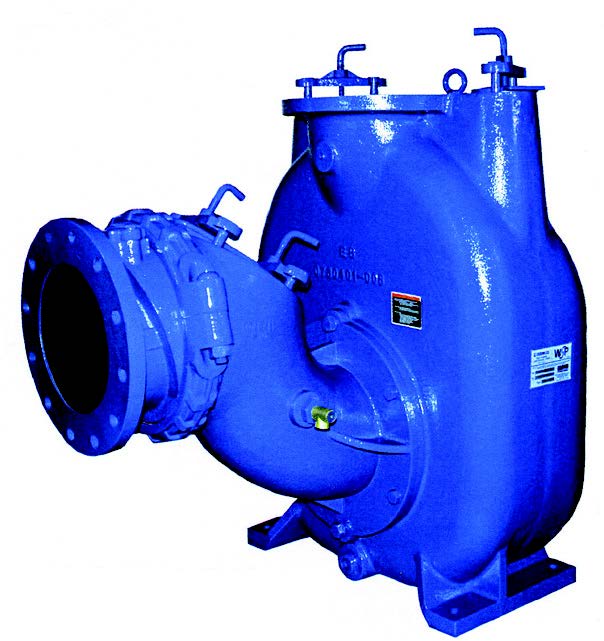
The Weir Self-Primer solids handling pump with Buzzsaw technology. (See reverse side for exploded
view and features.)
The process for upgrading each pump was simple. When a rotating assembly from the existing pump would go down, rather than rebuilding the assembly, a new WEMCO® Self-Primer rotating assembly and cover were swapped into the current pumps. This change out gave them the benefit of superior materials of construction like ductile iron over cast iron for the bearing housing, cast steel over ductile iron for the impeller, stainless steel 17-4PH over regular steel for the shaft, and a one-piece stainless steel impeller bolt instead of a steel bolt and washer. They also gained the patented self-cleaning Buzz Saw wear plate designed to dislodge materials as they become trapped on the impeller and moves them into the flow stream, reducing clogging of the pump. While there are many other benefits to the WEMCO® Self-Primer, like advanced safety features and an easily removable flap valve, it’s sometimes not economical or possible to replace a working pump. With that in mind WEIR made a superior product even more beneficial with the ability to upgrade competitors’ pumps.
Download the case study
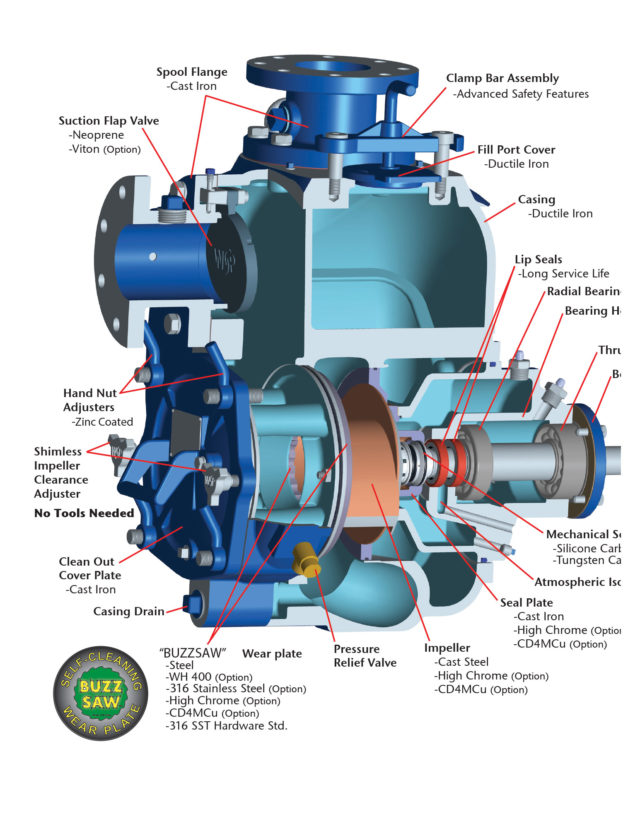
Case Studies
Huge Savings
Product reject rates dropped dramatically
APPLICATION
Chrome plating is a long, involved process and typically starts with degreasing, rinsing and cleaning, tedious polishing, then buffing, then acid dipping (etching), applying a metal catalyst then nickel and/ or copper plating (many times calling for multiple layers) prior to the chrome plating itself. Typically the parts are rinsed in between each process. As you can imagine, any particulate will show up as a defect and can’t be tolerated.
One auto parts manufacturer was encountering high costs and a severe problem with product reject rate. The rejects were due to particulate from their plating bath causing blemishes in the plating layer. The competitive bath filters were just not filtering their plating solutions properly and consistently.
This parts plant manager was furious with the problems they were having. Our rep, Jeff Bean, boldly stated he could solve their filtration problem.
During his process evaluation, Jeff discovered another filter issue. The existing filters, as received, would contaminate the baths and had to be pre-rinsed before they went into the filter vessels. This was a costly and tedious process.
Jeff immediately involved one of our premium filter suppliers, Pentair Engineered Filtration. Pentair was the perfect choice to develop the proper filter solution.
TESTING
At the heart of the problem solving was Pentair’s Technology Research Center (TRC) laboratory.
Pentair utilized sophisticated testing equipment to examine the existing filters being used.
It was found some of the filters ratings were dramatically different than the packaging indicated. (After testing their existing filter products, it was found that 0.5 micron filters were really 2.5 micron filters.) What micron filters were really needed?
After further discussions with the customer on the exact level of filtration required, Pentair test filters were furnished. After the initial tests were positive, additional Pentair filters were ordered.
RESULTS
- The Pentair filters could be installed right out of the box. No more pre-rinsing was required.
- The Pentair filters cleaned up the plating baths significantly better.
- Due to continued recirculation, the baths actually continued to improve over time.
- Product reject rates went down significantly.
- Filter life was comparable even with the much improved efficiency and repeatability.
- Filter element costs per filter were comparable to prior filters even with the improved filtration ability.
- $$$$ Thousands were saved due to lower scrap rate.
- The bottom line result was a competitive product with exceptional dirt holding capacities, precise filtration ratings, repeatable performance, low pressure drops, and high efficiencies.
Put our experience and knowledge to work toward solving your problems. Our solutions may save you a lot of time, money and headaches.
Call us today and let us know how we can help.
Download the case study
Case Studies
R. A. Ross & Associates team up with Neptune Chemical Co. to save a large power utility time and money
R. A. Ross & Associates and Neptune Chemical Pump Co. (A Dover Co., PSG-Pump Systems Group) provided a one-source solution to a tough pump and mixer system for ammonia and hydrazine
applications.
Our customer is one of the largest power utility companies in the U.S., providing electric and natural gas service to 4 million customers. This power utility needed chemical feed systems at their Noblesville, IN Generating Station that would deliver the proper amount of treatment chemicals used to prevent corrosion and help manage SO2 emissions. These chemicals include ammonia and hydrazine, chemicals that are not easy to deal with. R. A. Ross & Associates teamed up with Neptune Chemical Pump Co. ( a Dover Co., PSG-Pump Systems Group) to supply a complete package with every component and all equipment for the chemical metering system. This enabled our customer to shop and buy from one source, saving on engineering and contractor costs.
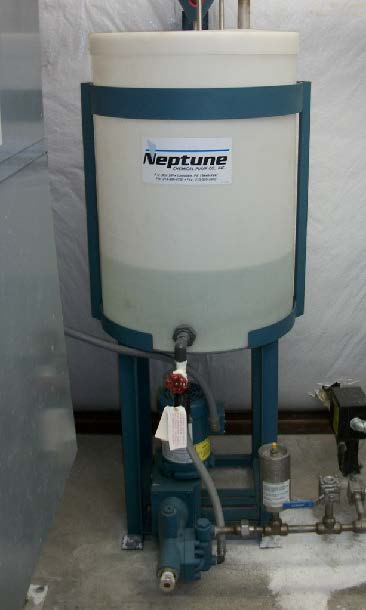
Neptune Chemical Co. Tank Mixer/Pump Package including:
• 50 Gallon polyethylene tank • Tank cover • 6150 HP Neptune Chemical Co. hydraulically activated pump • Mixer with electric or
air motor • Mixer bracket • PVC suction valve • Y strainer • Suction tubing • 1/2” Drain connection
Power utility mixes and pumps ammonia and hydrazine
The Noblesville, IN power utility generating station utilizes Neptune Chemical Co. Chemical Feed systems to deliver 19% ammonia and 35% hydrazine to their drum boilers. The ammonia is used to scrub SO2 from flue gas. Hydrazine is used to reduce dissolved oxygen to reduce corrosion. The power utility mixes (dilutes) and then meters each chemical by pumping to a central “mixing reservoir” combining the chemicals with demineralized water. At this point, a high-pressure hydraulically actuated Neptune Chemical Co. metering pump delivers the agents to:
- High pressure drum (800 PSI) and
- Low pressure drum (75 PSI)
Download the case study