The R. A. Ross team’s creative skills solve complex problem with innovative solution
Situation/Solution: A large oil company requested a Blackmer pump that would be used for “proving” gasoline, ethanol, diesel and biodiesel at several of their facilities. The specifications were listed as seen in the chart to the left.
The Ductile Iron Blackmer X4B 4” Sliding Vane Pump with Carbon vs. Iron. Viton mechanical seals met the specifications ideally running at 57% of maximum speed (which would give them long service life). The pumps would be coupled to Blackmer 5.77 to 1 HRB helical gear reducers with a 2.24 to 1 service factor for cool running operation and long reducer life. A 15 HP motor gave them more than sufficient safety margin.
Our job is to help keep you up and running.
R. A. Ross & Associates offers customers over 100 years combined experience with pumps and repairs.
-
-
Custom Blackmer trailer package built to customer requirements.
-
-
Trailer packages and the cart packages ready for customer delivery.
THE PROJECT SPECS:
Blackmer X4B Sliding Vane Pump assembly:
•Ductile iron construction
•Duravane vanes
•Viton o-rings
•Carbon vs. Iron mechanical seals
•Standard internal relive valve w/35-50psi spring
•4” NPT flange connections
•HRB 5.77:1 reducer to produce approx. 303rpm w/1750rpm motor
•15hp 3/60/230-460/1750 rpm Explosion Proof motor
•Formed steel base plate, couplings and guards
Trailer packing and control panel:
•5’ x 8’ 2990# capacity single axle utility trailer w/DOT approved lighting
•Tongue jack w/foot plate / tongue accepts 2” ball
•Jack on each rear corner for leveling/stability
•12ga. Treadplate steel floor
•2 – Wheel chock set and tool box w/lid and closure for storage
•Trailer dolly for movement of package by hand
BUILDING:
-
-
The treadplate steel floor gives us a solid base to start construction.
-
-
The pump is positioned on the trailer to keep the balance of the trailer and tongue weight as close as possible to its unloaded state.
-
-
Once the pump is secured to the deck, bracing and supports are added to accommodate the control panel. A tongue storage box is also added to house wheel chalks and provide additional storage.
-
-
Similar to the trailer packages the pump and control panel for the cart are installed to maintain maneuverability and ease of use.
-
-
Trailer packages and the cart packages ready for customer delivery.
-
-
The excess deck space around the pump leaves room for operator safety when attaching hoses to the pump and storage space for hoses to stay with the package.
RESULT:
Our client is very satisfied with not only our solution, but with the fact that we finished the project on time and under budget, and has ordered additional units from us.
Blackmer pumps are chosen in many cases as they are much “greener” (more energy efficient) than internal gear pumps. Blackmer vane pumps maintain their efficiency and flow even as the vanes wear where gear pumps start
losing flow and energy with any wear that occurs. The chart below shows the difference:
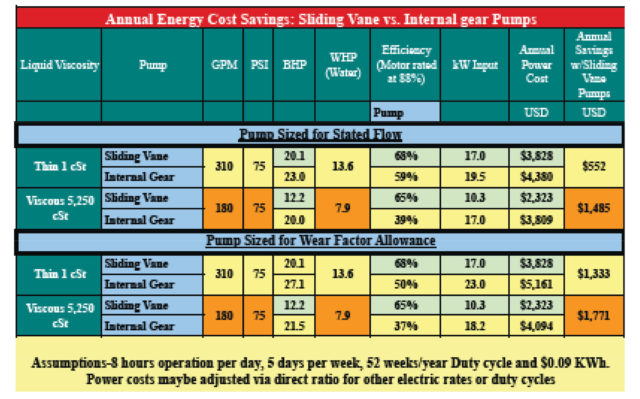
Blackmer X-Sliding Vane Pump typical applications:
Clean, non-corrosive industrial liquids and petroleum products, including fuel oils, lube oils, jet fuels, gasoline, edible oils, and a variety of solvents and thinners such as esters, ketones, naphtha’s, ethers, amines, aromatics, alcohol’s, terpenes, glycol’s and many other similar liquids.
Features and Benefits:
• Unique sliding-vane pump design self-adjusts for wear to maintain flow rates.
• Excellent self-priming and dry run capabilities.
• Blackmer mechanical seal and ball bearing construction provide maximum reliability.
• Symmetrical bearing support assures even loading and wear for long life.
• Adjustable relief valve protects pump against excessive pressures.
• External ball bearings are isolated from pumpage by mechanical seals to maximize bearing life and minimize contamination risk.
•Easy maintenance: vanes can be easily replaced without removing the pump from the piping system.
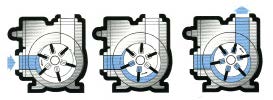
How Blackmer’s sliding vane action works
Blackmer’s positive displacement rotary pumps utilizing their unique sliding vane design offers the best combined characteristics of sustained high level performance, energy efficiency, trouble-free operation and low maintenance cost. Also, the high suction lift capability of these pumps makes them especially suitable for pumping from underground tanks, bulk plant service and aircraft refueling
Specially designed and built mobile Blackmer pump solution
Download the case study