Case Studies
Tough applications and regulations are right up our alley
A major petroleum refiner in the mid-west came to R.A. Ross & Associates for a positive dis-placement pump solution for crude oil transfer. The customer needed a robust pump that could not only handle the crude oil, but also the design of the pump had to meet the stringent American Petroleum Institute standards (API-676) for rotating equipment used in the petroleum refining process. Additionally, the pump had to meet U.S. Department of transportation (DOT) standards because it would be connected to piping in a DOT area. R.A. Ross & Associates was able to offer a solution from Blackmer Pump Company who manufactures a positive displacement screw pump which meets the API-676 and the DOT standards. In addition to the pump itself, all of the components of the pump assembly had to meet the API and DOT specification as well, from the motor to the mechanical seal, to the base. If you have a tough regulation or tough application, let R.A. Ross & Associates find an easy solution!
Blackmer Screw Pumps are ideally suited for:
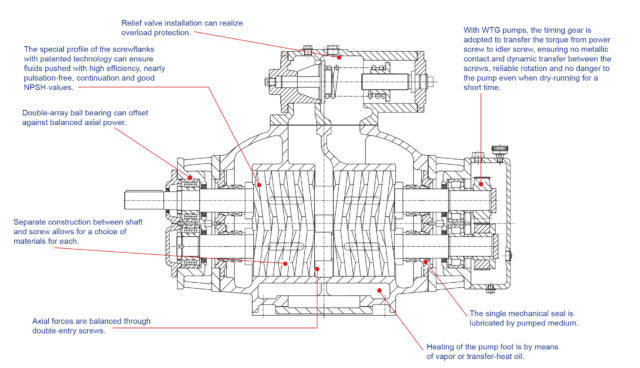
- Chemicals
- Caustics
- Adhesives
- Food & beverage
- Soap
- Petrochemicals
- Acids
- Polymers
- Crude oil
- Oilfields
- Asphalt
- Diesel
- Kerosene
- Lube oil
- Seawater
- Residuals
- Bulk transfer
- Loading/unloading
- Terminals
- Shipping
- Bilge and ballast
- Fire-suppression
How it works:
Blackmer Twin Screw Pumps are rotary, positive displacement pumps capable of handling various clean liquids that contain no solids.The pump is composed of two sets of opposed screws. During pump operation, the screws on the two shafts are engaged and form a sealed cavity with the surrounding pump casing.The pumped liquid is shifted axially as the screw shafts turn and steadily and constantly convey the liquid to the center of the pump where the discharge port is located. Since hydraulic forces on two screws are opposite and equal, the hydraulic axial stress on shafts is automatically balanced.
Download the case study
Case Studies
Ross solution saves customer $8,000 and 6 weeks on delivery
APPLICATION:
Cooling water at 220GPM @ 27’tdh Our customer had a KSB pump that was in need of replacement and had a quote in hand from a competitor for a pump assembly costing $10,000 with about an 8 week lead time. They requested we quote an alternative product that they could get within 4 weeks of ordering around the same price or better. We were able to do both beating the leadtime of the original quote by 6 weeks and price by almost $8000!
We didn’t have much to go on as we did not have any information on the KSB pump other than what was on the tag. Fortunately the tag had the process conditions of 220gpm @ 27’ tdh. We confirmed the conditions during onsite visits with the customer and provided our quote for the American Marsh 300 REC series pump based on these conditions.
The pump we proposed was a close coupled pump rather than a frame mounted configuration saving the customer precious space as the pump was going into some tight quarters. The American Marsh pump only required minimal piping changes to the existing system and the smaller size we provided gave the customer more flexibility in piping modifications. With The condition point required of the pump required a full diameter impeller and landed at 92.39% of the BEP also making this a much more efficient pump than the existing or competi-tor’s offering.
With an $8000 savings over the existing quote option the customer had, a lead time of 2 weeks, minimal piping changes required, improved efficiency, and standard pump features like carbon vs. silicon carbide mechanical seal and stainless steel fitted construction, the customer ordered 3 of the pumps deciding to replace all of the KSB pumps they had in this same service.
Download the case study
Resources, Summit Pumps
Some people still think they can align a pump with a straight-edge, in lieu of a laser or dial-indicator method. They are incorrect. While a straight-edge alignment can potentially kill your bearings, seals and couplings, it also consumes extra horsepower.
Recent studies show that a simple 0.050” offset, which is about the best straight-edge alignment possible, will consume 9% more power.
An angular misalignment of 0.015” gap per inch of shaft diameter will consume 6% more power.
At least once a month, we will receive a complaint that our pump is not aligned to the driver upon site arrival. We try to advise our distributors that the final alignment must be performed in the field. An initial rough alignment is done at the factory to prove that the unit is able to be aligned, but as the pump is transported, the unit will become out of alignment. Pump units should be alignment checked five different times during the course of the installation. (We will cover that subject another time.)
Also, note on existing installations you would never move the pump, only the driver. Although, on new installations before the piping is brought to the pump, it is perfectly acceptable and sometimes necessary to move the pump within the room allowed by the bolt holes.
-The Summit Pump Team
Learn More
Jim Elsey’s Pumps and Systems Articles
Resources, Summit Pumps
Did you know that when using an internal gear pump in applications above 225 degrees Fahrenheit or viscosities above 750 SSU, the pump may need extra clearances to operate properly? These extra clearances are applied to the rotor’s outer diameter, rotor’s inner diameter, the end clearance and (if applicable) the shaft or bracket bushing inner diameter.
In high temperature applications, the extra clearances are needed to allow for expansion of the materials. As a manufacturer, calculations for the clearances are controlled by material selections and are determined based upon a specific material combination within the pump. Changing the part’s materials could change the amount of extra clearances needed for the pump.
High viscosity applications need the extra clearance to allow the fluid to pass through which keeps the pump from reaching its maximum allowable horsepower limit. If these clearances where not applied, excessive wear or failure of the pump would be premature.
This is just one reason why it is of the utmost importance to collect the application’s fluid and process properties to keep your pump’s life at a maximum.
Click here to download our Application Data Sheets.
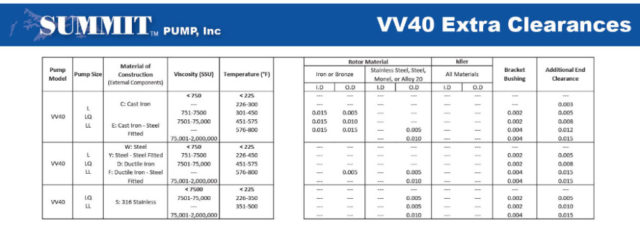
Click here for the VV40 and VV95 extra clearance documents.
-The Summit Pump Team
Learn More
Jim Elsey’s Pumps and Systems Articles
Resources, Summit Pumps
Each of Summit Pump’s Internal Gear Pumps come standard with a pressure relief valve. These valves are designed and positioned to protect the pump by SAFETY means only; they are not meant for throttling the flow or pressure of the system.
When the system pressure is increased and the pressure relief valve is opened, possibly due from a blocked pipe or closed valve, it recirculates the fluid within the pump via the valve. Even though this avoids building pressure in the system.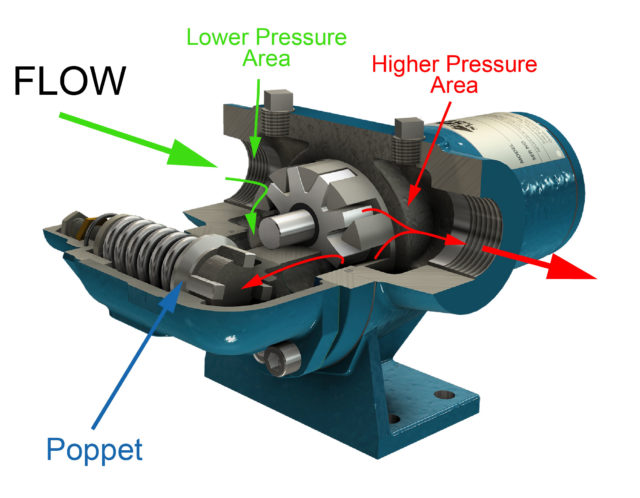
The heat generated by the moving parts of the pump has nowhere to go, except into the pump materials and the recirculating fluid. This can become problematic for a few reasons:
- The pump materials expand, closing the specially designed clearances for the application, pump, model and size potentially causing the pump to lockup.
- The vapor pressure of the fluid increases, lowering the NPSHa past NPSHr causing the pump to cavitate, causing damage to the casing, rotor and/or idler.
- The fluid flashes in the valve. This means the fluid rapidly expands potentially exploding the pump and/or valve. This is even more critical with fluids with low boiling points (saturation temperatures), such as propane or ammonia, as flashing will happen at lower temperatures, depending on suction pressure.
There should always be other means of pressure relief in the system. Switches and alarms should also be installed if the pressure relief valve to were ever open. Measuring flow in the discharge is a good way of doing this.
The valves are set to a standard pressure based on the pump model and size, unless otherwise specified on your purchase order.
–The Summit Pump Team
Learn More
Jim Elsey’s Pumps and Systems Articles