Case Studies
CASE STUDY
Problem: Small non-electric pump needed to remove water from mine shafts.
Ross & Associates solves problem of high cost of removing water from mine shafts
A western KY coal mine was looking for a small, portable, non-electric pump to remove water from mine shafts. The electric pumps that they would typically use for dewatering were cost prohibitive due to the IMSHA explosion proof safety guidelines that all mine operations must adhere to. Since air lines were already in the mine for drilling tools and other equipment, an ARO air operated diaphragm pump was an easy choice. We were able to supply a small 1” ARO pump that suited the customer’s needs perfectly. Word quickly spread to other mining operations in the area which generated more sales of the ARO product.
Our job is to help keep you up and running.
R. A. Ross & Associates offers over 150 years combined experience.
Ingersoll Rand ARO offers a wide range of fluid technologies for today’s demanding industries and applications.
Diaphragm Pumps
- Aluminum, Cast Iron, Stainless Steel, Hastelloy-C
- Groundable Acetal, PVDF (Kynar), Polypropylene
- 1/4” to 3” ported • Flow rates up to 275 gpm
- Santoprene, Hytrel, PTFE, Viton, Nitrile
|
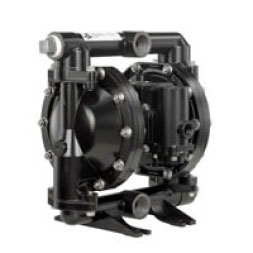 |
Diaphragms Piston Pumps
- Carbon Steel, Stainless Steel
- 2-Ball, 4-Ball, Chop-Check, Oil & Grease Pumps
- Pressure ratios up to 65:1 (100:1 for grease pumps)
- Flow rates up to 32.8 gpm
- UHMW-PE, PTFE, and Leather Packing seals available
|
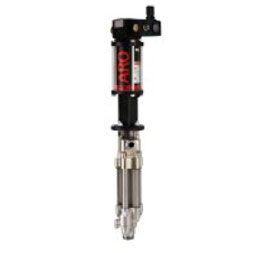 |
Specialty Application Pumps
- Pit Boss ™ Dewatering Pumps (1 1/2” – 3” ports)
- Powder Transfer Pumps (2” & 3” ports)
- Flex-‐Check™ Pumps (3/8” ports)
- Sanitary Transfer Pumps (1” – 3” ports)
|
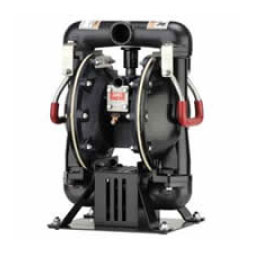 |
Pneumatic Valves & Cylinders
- 2 way, 3 way, & 4 way valves
- Up to 1” ports
- Pilot, solenoid, and/or mechanical actuators & returns
- Single-‐ and double-‐acting cylinders
- Up to 10” bore, various stroke lengths available
- Aluminum, Stainless Steel
|
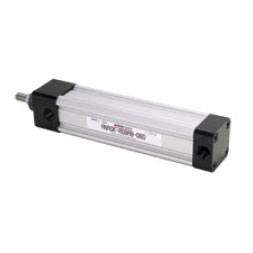 |
Download the case study
Case Studies
Satisfied R. A. Ross and Associates customer using Ingersoll Rand Aro pumps for over 20 years
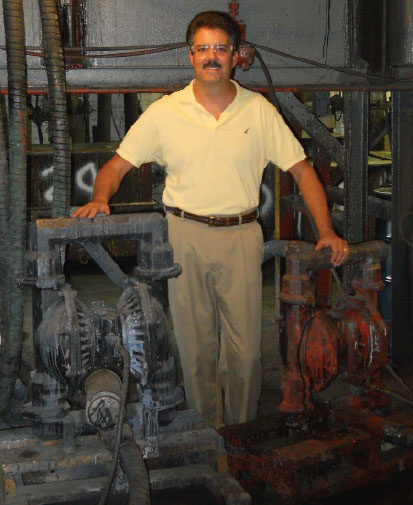
Steve Marcus, VP Marcus Paint Company, with two of the many I-R Aro Pumps they use.
Marcus Paint has been manufacturing paint since 1853 and supplies coatings to industrial companies all over the US and Mexico.
We manufacture paint for every kind of product you can think of, metals, plastic, etc., and, as you can imagine, mixing different resins and pigments requires many different solvents.
Solvent temperatures vary from 35º to 185º. That can tear up diaphragms. I-R Aro pumps can stand up to that kind of abuse.
Without pumps, we shut down. Pumps are vital to mixing paints.
“We pump several different types of solvents. Solvent temperature extremes tear up diaphragms. Aro Pumps and Ross & Associates solved our problems. No more pump failure.”
- Marcus Paint pumps from 500 to 6,000 gallons of paint daily
- Marcus Paint has used Aro Pumps since 1988
CASE STUDY INSIDE
Paint manufacturer says; “Without pumps, we shut down.” How reliable are your pumps?
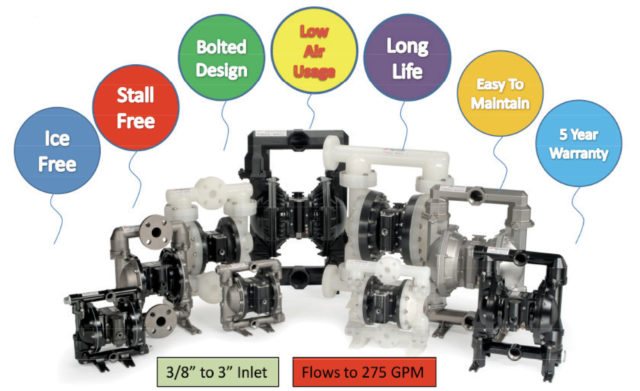
WHY INGERSOLL RAND ARO PUMPS?
Only I-R Aro Pumps can stand up to the abuse that companies like Marcus Paint Company put them through. Aro Pumps are designed to handle extreme temperature differences, various chemicals and still operate round the clock. Less down time means more profit to any company’s bottom line.
Download the case study
Case Studies
Tough applications and regulations are right up our alley
A major petroleum refiner in the mid-west came to R.A. Ross & Associates for a positive dis-placement pump solution for crude oil transfer. The customer needed a robust pump that could not only handle the crude oil, but also the design of the pump had to meet the stringent American Petroleum Institute standards (API-676) for rotating equipment used in the petroleum refining process. Additionally, the pump had to meet U.S. Department of transportation (DOT) standards because it would be connected to piping in a DOT area. R.A. Ross & Associates was able to offer a solution from Blackmer Pump Company who manufactures a positive displacement screw pump which meets the API-676 and the DOT standards. In addition to the pump itself, all of the components of the pump assembly had to meet the API and DOT specification as well, from the motor to the mechanical seal, to the base. If you have a tough regulation or tough application, let R.A. Ross & Associates find an easy solution!
Blackmer Screw Pumps are ideally suited for:
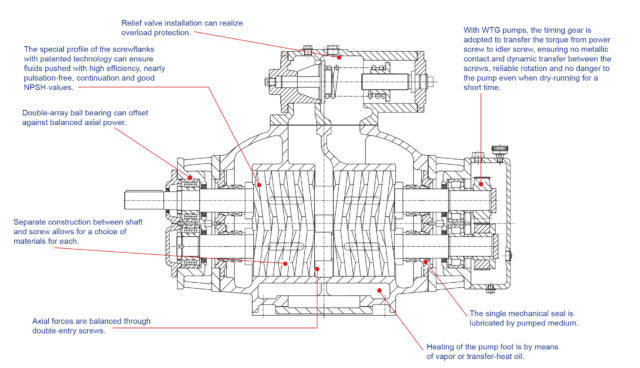
- Chemicals
- Caustics
- Adhesives
- Food & beverage
- Soap
- Petrochemicals
- Acids
- Polymers
- Crude oil
- Oilfields
- Asphalt
- Diesel
- Kerosene
- Lube oil
- Seawater
- Residuals
- Bulk transfer
- Loading/unloading
- Terminals
- Shipping
- Bilge and ballast
- Fire-suppression
How it works:
Blackmer Twin Screw Pumps are rotary, positive displacement pumps capable of handling various clean liquids that contain no solids.The pump is composed of two sets of opposed screws. During pump operation, the screws on the two shafts are engaged and form a sealed cavity with the surrounding pump casing.The pumped liquid is shifted axially as the screw shafts turn and steadily and constantly convey the liquid to the center of the pump where the discharge port is located. Since hydraulic forces on two screws are opposite and equal, the hydraulic axial stress on shafts is automatically balanced.
Download the case study
Case Studies
Ross solution saves customer $8,000 and 6 weeks on delivery
APPLICATION:
Cooling water at 220GPM @ 27’tdh Our customer had a KSB pump that was in need of replacement and had a quote in hand from a competitor for a pump assembly costing $10,000 with about an 8 week lead time. They requested we quote an alternative product that they could get within 4 weeks of ordering around the same price or better. We were able to do both beating the leadtime of the original quote by 6 weeks and price by almost $8000!
We didn’t have much to go on as we did not have any information on the KSB pump other than what was on the tag. Fortunately the tag had the process conditions of 220gpm @ 27’ tdh. We confirmed the conditions during onsite visits with the customer and provided our quote for the American Marsh 300 REC series pump based on these conditions.
The pump we proposed was a close coupled pump rather than a frame mounted configuration saving the customer precious space as the pump was going into some tight quarters. The American Marsh pump only required minimal piping changes to the existing system and the smaller size we provided gave the customer more flexibility in piping modifications. With The condition point required of the pump required a full diameter impeller and landed at 92.39% of the BEP also making this a much more efficient pump than the existing or competi-tor’s offering.
With an $8000 savings over the existing quote option the customer had, a lead time of 2 weeks, minimal piping changes required, improved efficiency, and standard pump features like carbon vs. silicon carbide mechanical seal and stainless steel fitted construction, the customer ordered 3 of the pumps deciding to replace all of the KSB pumps they had in this same service.
Download the case study
Case Studies
How we operate our company can help your bottom line.
CASE STUDY ONE
Multiply that by how many pumps they are running and you come up with some significant savings.
But more importantly, we now have a customer who knows we aren’t in this business to make a quick sale. We value relationships that, like some of our customers, have lasted 35 years. We look at the best solution that will be the least costly over time.
We have quite a few case studies on our website that share how we have solved problems and saved customers not only money, but down time as well.
Our job is to keep you up and running
CASE STUDY TWO
R. A. Ross & Associates has nearly 200 years combined experience
How we saved an auto parts supplier hundreds of thousands of dollars
Chrome plating is a long, involved process and typically starts with degreasing, rinsing and cleaning, tedious polishing, then buffing, then acid dipping (etching), applying a metal catalyst then nickel and/or copper plating (many times calling for multiple layers) prior to the chrome plating itself. Typically the parts are rinsed in between each process.
As you can imagine, any particulate will show up as a defect and can’t be tolerated.
One auto parts manufacturer was encountering high costs and a severe problem with product reject rate. The rejects were due to particulate from their plating bath causing blemishes in the plating layer. The competitive bath filters were just not filtering their plating solutions properly and consistently.
We immediately involved one of our premium filter suppliers, Pentair Engineered Filtration. Pentair proved to be the perfect choice to develop the proper filter solution.
RESULTS
- Hundreds of thousands of dollars were saved due to lower scrap rate.
- The bottom line result was a competitive product with exceptional dirt holding capacities, precise filtration
ratings, repeatable performance, low pressure drops, and high efficiencies. Put our experience and knowledge to work to¬ward solving your problems. Our solutions may save you a lot of time, money and headaches.
Download the Case Study