Case Studies
Whatever it takes.
How the R. A. Ross team knowledge and experience can help you.
Process technology training provides valuable information for industrial engineering firm
“I knew some of these types, but it was new exposure for me on the other half of the list”
– Todd Hess, Vice President and
Senior Designer
with Hess Engineering
Sometimes, the very solution you need for a complex process may involve a technology that you may never have heard of. Engineers are often called upon to design complicated systems in industrial and municipal processes that require a specific type of pump or piece of equipment.
That’s where R.A. Ross & Associates can help!
We’ve put together a training module covering the various types of pump technologies available today and the typical applications they are best suited for. We provided our Process Technology class during a “lunch and learn” at the well respected firm of Hess Engineering (formerly A.J. Hess & Associates) in Calvert City, KY. Hess Engineering has been around since 1984 and provides civil, mechanical, electrical, chemical engineering and project management services in Western Kentucky and surrounding areas.
Contact us today to set up your class and see what you might be missing!
Some of the types of pumps covered in our training class:
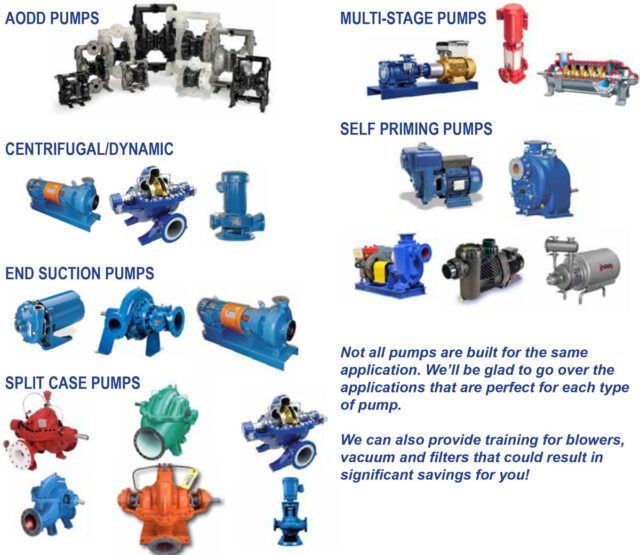
Personal Development Hours Certificate Training
We also provide a PDH (personal development hours) Certificate upon completion of the training.
Download the case study
Case Studies
Doing whatever it takes.
The Ross team provides tough pumps for tough applications!
If you need it, Team Ross has it!
PROBLEM/SOLUTION:
A global automotive plating company with operations in Eastern Kentucky needed some rugged pumps for a rinse water application that would be required to handle a mixture of aggressive chemicals.
The existing pumps in service couldn’t hold up to the various chemicals present in the rinse water. After review of the application, the R.A. Ross team had the perfect solution in mind; the Vanton® Chem-Gard® ANSI centrifugal pump with PVDF (Kynar) wetted materials with clean water flush to protect the seal.
Wet end components of Vanton CHEM-GARD® centrifugal pumps are injection molded of corrosion resistant polypropylene (PP), polyvinyl chloride (PVC), chlorinated polyvinyl chloride (CPVC), polyvinylidene fluoride (PVDF), ethylene chlorotrifluoroethylene (ECTFE) or other non-metallic materials that are 100% inert to the fluids being handled across the entire pH range. This eliminates the corrosion and failure associated with pumps constructed of stainless steel and other alloys, the wicking associated with fiberglass pump components and the delaminating inherent with plastic-lined metal pumps.
Application info:
Transfer of corrosive rinse water at the following rates: 100 GPM @ 40’ TDH
Vanton Chem-Gard® ANSI-Centrifugal pump model CGA-KY-3x2x8
- Horizontal centrifugal with all fluid contact parts of homogeneous non-metallic materials, dynamically balanced keyed semi-open impeller, stainless steel shaft with wet end sleeved with PVDF (Kynar).
- Materials of Construction PVDF / Kynar
- Impeller Dia. 8”
- Suction and Discharge 3” x 2” 150# flanged
- Mechanical Seal
- Water Jacket Standard (Seal water supply & drain required).
- Pedestal Guard Polyethylene
- 5 HP, 230-460 volt / 3-phase / 60-Hz, 1800 RPM, TEFC, severe duty motor mounted on an epoxy coated, steel base plate including spacer coupling and coupling guard 400 GPM @ 70’ THD
Vanton Chem-Gard® ANSI-Centrifugal pump model CGA-KY-4x3x10
- Horizontal centrifugal with all fluid contact parts of homogeneous non-metallic materials, dynamically balanced keyed semi-open impeller, stainless steel shaft with wet end sleeved with PVDF (Kynar).
- Materials of Construction PVDF / Kynar
- Impeller Dia. 10”
- Suction and Discharge 4” x 3” 150# flanged
- Mechanical Seal
- Water Jacket Standard (Seal water supply & drain required)
- Pedestal Guard Polyethylene
- 20 HP, 230-460 volt / 3-phase / 60-Hz, 1800 RPM, TEFC, severe duty motor mounted on an epoxy coated, steel base plate including spacer coupling and coupling guard
The Vanton Chem-Gard ®pump used in this case study:
- Flows to 1150 GPM (261 m3/h)
- Heads to 185 ft (56 m)
- Temps to 275°F (135°C)
- Construction: PP, PVDF
Download the case study
Case Studies, Featured
A case study in how to transfer liquified gases (propylene, in this application) using the vapor itself.
Custom-built, explosion proof Blackmer compressor package exceeded our customers expectations!*
There are challenges when transferring liquids that are vapors at atmospheric pressures. Liquids like ammonia, butadiene, propane, propylene, refrigerants, or vinyl chloride must be contained under pressure to keep them in equilibrium. Pumps, with the limited Net Positive Suction Head available (NPSHA), cavitate and can become vapor locked.
Using Blackmer HD gas compressors to compress the vapor to transfer the product is much more efficient. Transfer faster and recover much more product with the Blackmer HD compressor.
A global chemical manufacturer (and their engineering firm) asked for “Liquid transfer of propylene from a 435 lb. cylinder to a 125 gallon storage tank and transfer from the storage tank to a feed tank”. Conditions: 20F, 57 psi inlet pressure/77 psi discharge pressure; 70F, 140 psi inlet pressure/166 discharge pressure; and 100F, 210 psi inlet pressure/230 discharge pressure thus the compressor was going to see varying conditions although the differential pressures (discharge minus suction) were pretty constant at 20 psid to 26 psid.
Using a Blackmer compressor for liquid transfer and vapor recovery
How it works:
LIQUID TRANSFER
The compressor and 4 way valve is configured to allow the destination vessel vapor to enter the compressor where the gas is slightly compressed and discharged to the top of the source container or vessel where the gas pushes on the top of the liquid forcing the liquid up the liquid line connected to the bottom of destination vessel.
LIQUID BOIL OFF AND VAPOR RECOVERY
When nearly all the product is transferred, you are left with a small amount (heel) at the bottom. You then change the 4 way valve and other valves to allow the vapor line from the source vessel to connect to the compressor inlet and you compress that gas and push it up through the bottom of the destination vessel. As the gas travels up through the liquid, it cools and tends to condense into liquid. This operation continues until the pressure in the source vessel drops to a pre-set point (typically dictated by economics).
The compressor transfer process described is done with many liquified gases and natural gas with the same basic process steps.
As a long-time distributor for Blackmer, we were able to provide a Blackmer gas compressor package for this important application.
Our design team assembled a complete package in our Louisville facility per the customers requirements from the ground up, including a custom steel base with forklift portability, and a complete controls package for “plug and play” installation.
* Our customer asked for 15 minute liquid transfer and we did it in about 5 minutes!
Backside of Nema 7 control panel showing Nema 7 controls which were prewired and connected to compressor and panel.
Application details:
Liquified gas transfer of propylene from 435-gal cylinder to 125-gal storage tank and transfer from storage tank to feed tank. 4 SCFM @ 77 PSIG, 166 PSIG and 231 PSIG.
Custom compressor package:
- Blackmer heavy-duty compressor model HD082B (Blackmer’s smallest HD size) – non-lubricated, 1-stage, vertical, air cooled, single cylinder, single acting, ductile-iron construction with packing.
- 76”x26” structural steel baseplate with V-belt drive, belt-guard, motor slide base, liquid trap, 4-way valve and strainer.
- 3-HP, 1750 RPM, 182T frame explosion proof motor, belt drive.
- NEMA7 Low oil pressure switch, low suction pressure switch, high discharge pressure switch, high temp switch and SS high liquid level float switch.
- Discharge relief valve ASME.
- Mounted and wired NEMA 7 control panel with start/stop push button, Power “on” light, Production test report and hydrostatic test @ 503 PSIG.
Blackmer heavy-duty compressor model HD082B mounted on structural steel baseplate.
Case Studies
Our solution will save a customer over $80,000 a year for just ONE drying operation.
Big savings by less compressed air usage for drying parts
SITUATION
Compressed air is often referred to as the “third utility” in industrial plants as the cost to produce it can be extremely high. Many companies use compressed air to blow off or dry parts during certain stages of the manufacturing process. Large air compressors are expensive to purchase and maintain not to mention the cost of compressed air delivery equipment (ie, high pressure hoses, air knives, blades and nozzles, etc.) used to get the air to the process. R.A. Ross and Associates was able to bring an air savings solution to a major brake pad manufacturer in Kentucky by recommending the use of regenerative air blowers instead of compressed air to dry parts. Regenerative air blowers produce a higher volume of air at a lower pressure at the same time using less energy. The cost savings to the customer by switching to the regenerative blower and air knife system for one drying operation came to approximately $80,000 per year*. Equipment payback was about 9 weeks. That’s a serious solution! And at R.A. Ross & Associates, that’s what we do everyday!
HOW IT WORKS
Since each product and application is unique, Republic Blowers will ask that you fill out an Evaluation Guide (example below) detailing size of product, description of product, (holes, shape, etc.), speed of conveyor belt and so on. Once your specific need is determined, a custom designed air knife system will be recommended. Once approved, we will then test and be able to determine the amount of savings over traditional compressed air operations.
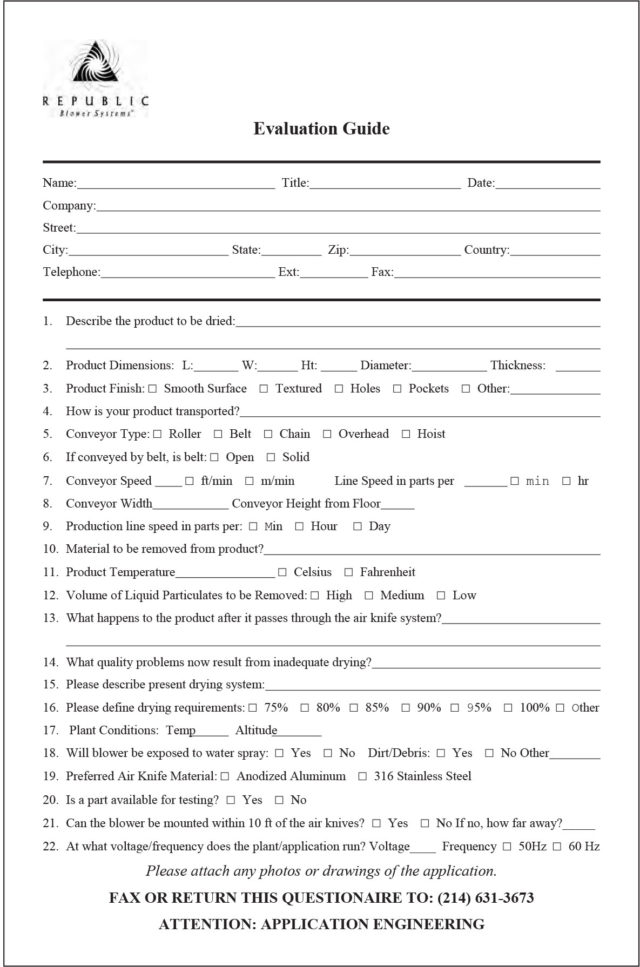
REPUBLIC MANUFACTURING AIR KNIFE SYSTEMS
• Custom designed and manufactured
• Perfect for: Drying parts, bottles, cans, food products, packaging,fruits, vegetables, meat, fish, poultry, textiles, carpet,film, wire, cable, metal, tile, wood, flooring
•Belt cleaning: Debris removal, sawdust removal, confectioner and food topping removal, liquid blow-off
•Static control
•Air curtain: Prevent hot air loss from oven, prevent cold air loss from freezer
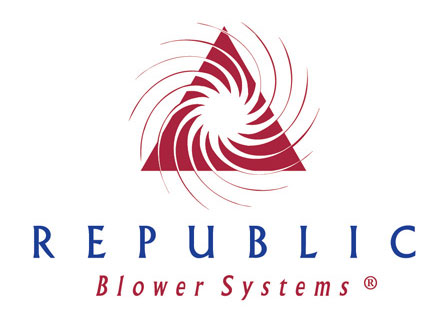
Over $80,000 per year compressed air savings!
Case Studies
Problem:
A major chemical manufacturer in Southern Indiana was having an issue with premature diaphragm failures on a chemical transfer operation.
The diaphragms in a competitors air operated double-diaphragm (AODD) pump were failing after only a short time in operation.
In this harsh application, the pumps are required to transfer chemicals from totes to other process-es in the plant. The operators must work quickly between batches and the pumps are required to pump several different chemicals each day.
After visiting with the customer and seeing the operation, it was surmised that the reason for the premature diaphragm failures was over-pressurization on the air supply and water hammer or back pressure spikes from the rapid opening and closing of valves at the beginning and end of pumping cycles.
Solution:
Our team came up with the following solution; we recommended a custom package comprised of a 1.5” ARO® AODD pump in 316SS and Teflon construction with ARO® Long Life® Teflon diaphragms, an ARO® air line kit complete with air hose, air pressure regulator/filter with gauge and a 1.5” NPT, 316SS/Teflon pulsation damp-ener manufactured by Blacoh®.
Additionally, this equipment was offered on a 60-day trail basis. The customer has experienced a significant increase in diaphragm life with this system in place.
If you have a troublesome application, let us provide a solution for you!
Custom diaphragm pump package model info:
- 1.5” ARO®, air-operated, double diaphragm pump model PD15A-ASS-STL
- ARO® air line connection kit w/ARO® filter-regulator and gauge for air pressure control
- 1.5” Blacoh® pulsation dampener model AOD-15-NPT
Case Studies
The R. A. Ross team goes above and beyond to keep you up and running.
Whatever it takes.
Heat exchanger plates and gaskets needed NOW!
Problem/Solution:
Our customer was in need of 14 plate and Nitrile gasket sets for its heat exchanger.
The customer, whose primary function is the application of corrosion-resistance coatings for all types of metals for the automotive industry, was unable to operate without its heat exchanger and would be down until the exchanger was brought back into service.
The customer requested that we supply these parts TODAY, and indicated they would be willing to drive to pick up the parts if we could locate the correct parts for their heat exchanger. While we don’t stock parts for heat exchangers, we made numerous phone calls until we were able to work with one of our supplier’s in Tennessee that not only had the parts in stock, but was able to have the order available for pick up within a few hours. What normally would take at least a day to get delivered with expedited delivery was available to the customer and they were able to get their operations back on track within the same day. This “Whatever it takes” attitude by our team is how we operate every day, no matter how large or how small the order.
In addition to plates and gaskets for heat exchangers, we stock or can order parts, part kits and drop in replacements for the following brands of pumps, blowers and vacuum.
Abaque
Ahlstrom
Allis-Chalmers
All-Prime
Allweiler
American Marsh
American
Wellworks
Ansimag
ARO
Aquflow
Aurora
Becker
Bingham
Blackmer
Black-Clawson
Boerger
Bornemann
Busch
Chicago
Clow
Cornell
Crane
Crane Deming
Dean
Dekker
DeLaval
Deming
Dickow |
Durco
Envirogear
Fairbanks Morse
Finish-Thompson (FTI)
Flowserve
Floway
Galigher
Gardner-Denver
Gorman-Rupp
Goulds
Graco
Griswold
HCP
Hidrostal
Ingersoll-Dresser
Pump (IDP)
Ingersoll-Rand
ITT
Kinney-Vacuum
Lobee
LMI
MDM
Mono
Monoflo
Morris
Moyno
MTH
Nash |
Neptune
Netzsch
Paco
Patterson
PCM
PeerlessPioneer
Robbins & Meyers
RoperRoto-Jet
Seepex
Sethco
Smith & Loveless
Sulzer
Summit
Sundyne
Tarby
Vanton
Verderflex
Vertiflo
Viking
Warman
Warren
Warren-Rupp
Watson-Marlow
Wemco
Wilden
Worthington
Yamada
Yeomans |