When NOT to use a pump for liquid transfer.
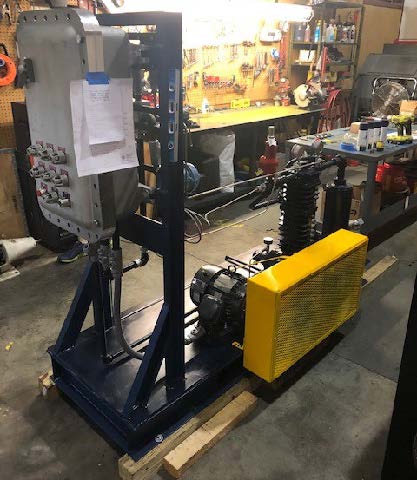
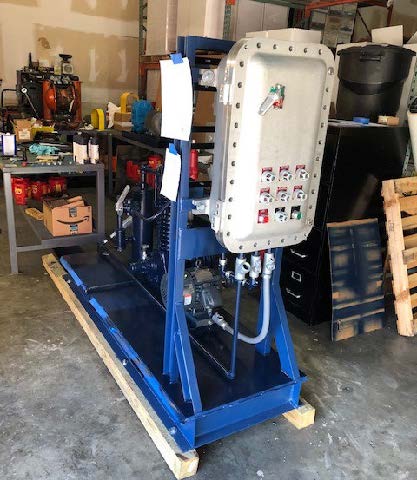
A case study in how to transfer liquified gases (propylene, in this application) using the vapor itself.
Custom-built, explosion proof Blackmer compressor package exceeded our customers expectations!*
There are challenges when transferring liquids that are vapors at atmospheric pressures. Liquids like ammonia, butadiene, propane, propylene, refrigerants, or vinyl chloride must be contained under pressure to keep them in equilibrium. Pumps, with the limited Net Positive Suction Head available (NPSHA), cavitate and can become vapor locked.
Using Blackmer HD gas compressors to compress the vapor to transfer the product is much more efficient. Transfer faster and recover much more product with the Blackmer HD compressor.
A global chemical manufacturer (and their engineering firm) asked for “Liquid transfer of propylene from a 435 lb. cylinder to a 125 gallon storage tank and transfer from the storage tank to a feed tank”. Conditions: 20F, 57 psi inlet pressure/77 psi discharge pressure; 70F, 140 psi inlet pressure/166 discharge pressure; and 100F, 210 psi inlet pressure/230 discharge pressure thus the compressor was going to see varying conditions although the differential pressures (discharge minus suction) were pretty constant at 20 psid to 26 psid.
Using a Blackmer compressor for liquid transfer and vapor recovery
How it works:
LIQUID TRANSFER
The compressor and 4 way valve is configured to allow the destination vessel vapor to enter the compressor where the gas is slightly compressed and discharged to the top of the source container or vessel where the gas pushes on the top of the liquid forcing the liquid up the liquid line connected to the bottom of destination vessel.
LIQUID BOIL OFF AND VAPOR RECOVERY
When nearly all the product is transferred, you are left with a small amount (heel) at the bottom. You then change the 4 way valve and other valves to allow the vapor line from the source vessel to connect to the compressor inlet and you compress that gas and push it up through the bottom of the destination vessel. As the gas travels up through the liquid, it cools and tends to condense into liquid. This operation continues until the pressure in the source vessel drops to a pre-set point (typically dictated by economics).
The compressor transfer process described is done with many liquified gases and natural gas with the same basic process steps.
As a long-time distributor for Blackmer, we were able to provide a Blackmer gas compressor package for this important application.
Our design team assembled a complete package in our Louisville facility per the customers requirements from the ground up, including a custom steel base with forklift portability, and a complete controls package for “plug and play” installation.
* Our customer asked for 15 minute liquid transfer and we did it in about 5 minutes!
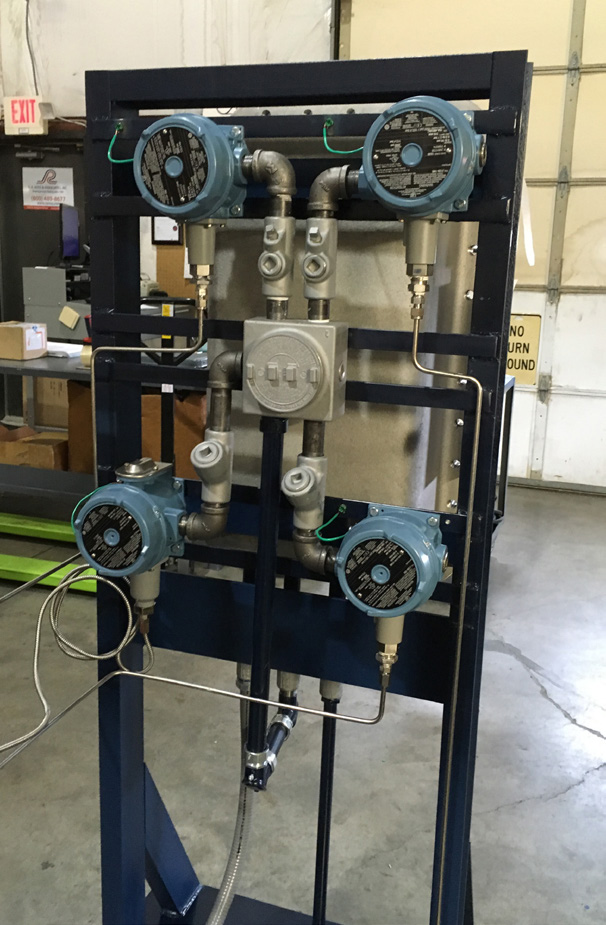
Backside of Nema 7 control panel showing Nema 7 controls which were prewired and connected to compressor and panel.
Application details:
Liquified gas transfer of propylene from 435-gal cylinder to 125-gal storage tank and transfer from storage tank to feed tank. 4 SCFM @ 77 PSIG, 166 PSIG and 231 PSIG.
Custom compressor package:
- Blackmer heavy-duty compressor model HD082B (Blackmer’s smallest HD size) – non-lubricated, 1-stage, vertical, air cooled, single cylinder, single acting, ductile-iron construction with packing.
- 76”x26” structural steel baseplate with V-belt drive, belt-guard, motor slide base, liquid trap, 4-way valve and strainer.
- 3-HP, 1750 RPM, 182T frame explosion proof motor, belt drive.
- NEMA7 Low oil pressure switch, low suction pressure switch, high discharge pressure switch, high temp switch and SS high liquid level float switch.
- Discharge relief valve ASME.
- Mounted and wired NEMA 7 control panel with start/stop push button, Power “on” light, Production test report and hydrostatic test @ 503 PSIG.
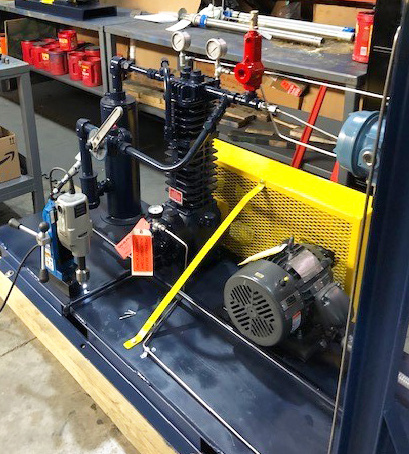
Blackmer heavy-duty compressor model HD082B mounted on structural steel baseplate.