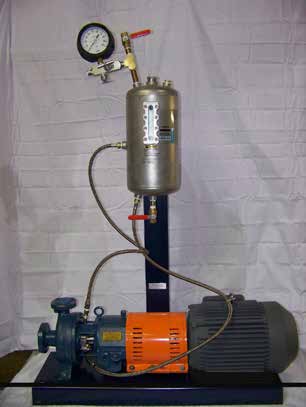
Dean pH2111 1×1.5×6 in 316ss construction 7.5hp EXP motor ASI model 595 double mechanical seal API Plan 53 barrier tank setup Custom pump base with seal pot stand to keep the package compact. Note: This package was developed in 2009 and is working so well after 8 years the customer just ordered a duplicate package!
CASE STUDY
Refinery uses Dean and ASI for sodium hydrogen sulfide (NaHS) application
Problem: Pump seals leak sodium hydrogen sulfide into atmosphere.
Solution: The raw gas sulfur knockout process at a local refinery produces sodium hydrogen sulfide (NaHS) and must be circulated through the tank to keep particles in suspension. The particulate can be anywhere from the size of a grain of sand to the size of a pencil eraser. Luckily the particles are easily deformable with the consistency of wet cereal making a centrifugal pump an acceptable means of transfer. The problem is the sealing of the pump. The product has a tendency to crystallize and the customer did not want any leakage of the product to atmosphere. For our application the customer chose to use a double seal with an API Plan 53 setup. In this setup a pressurized seal pot is used to isolate the product from atmosphere. The barrier fluid is contained in a seal pot which is pressurized to a higher pressure than the pump seal chamber. Barrier fluid must be compatible with the process fluid as there will always be some leakage of the barrier fluid into the process fluid.